Product Description
DC-C15 is a kind of room temperature vulcanized silicone rubber in condensation type. It’s generally named as two part silicone rubber , Part A is a flowable liquid silicone, Part B is the curing agent (Tin catalyst) . It’s mainly used for mold making.
DC-C15 Silicone rubber are kinds of soft silicone with good fluidity ,its suitable for small size product with detailed pattern by pouring operation, especially popular for the manufacturer of very small resin crafts and candle decorations .
DC-C15 silicone rubber is used for making molds of concrete stone, Tire ,GRC, gypsum decoration, plaster ornaments, fiberglass products, polyester decoration, unsaturated resin crafts, polyresin crafts, polyurethane, bronze, wax, candle, tire molds and similar products.
DC-C15 silicone rubber has low Shrinkage, high tensile and tear strength, high temperature resistance, high duplication times, is quite excellent for the decorative candle molding.
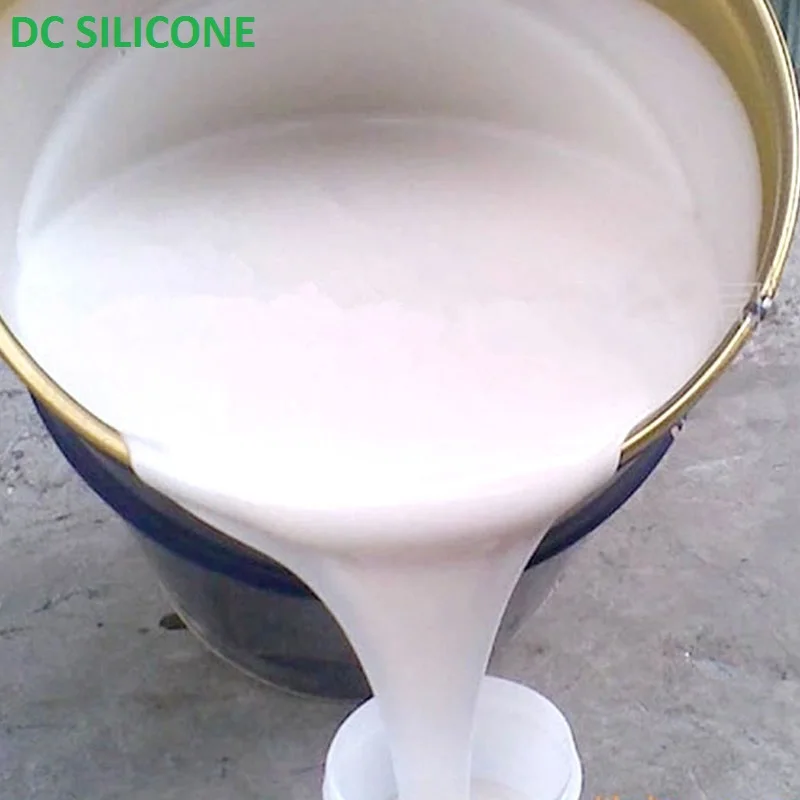
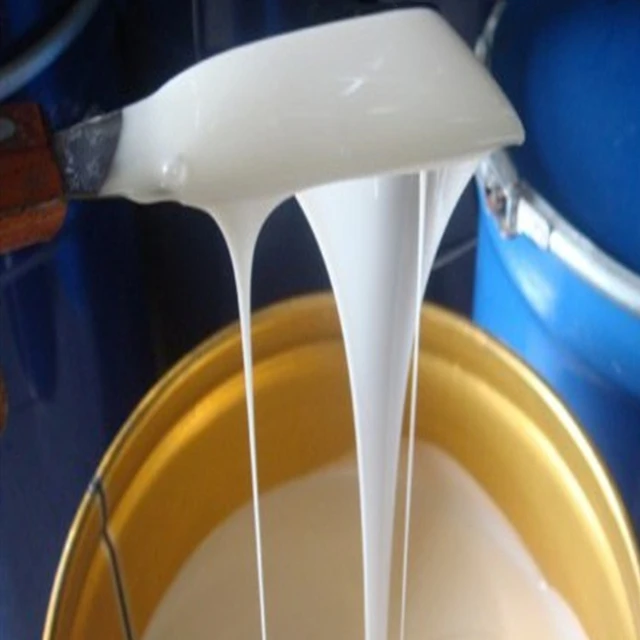
Technical Parameters
DC-C15 Silicone rubber are kinds of soft silicone with good fluidity ,its suitable for small size product with detailed pattern by pouring operation, especially popular for the manufacturer of very small resin crafts and candle decorations .
|
|
Mixing ratio (%) |
Pot life (mins,
under 25℃)
|
Curing time
(hrs,under 25℃ )
|
|
Tensile-
strength (MPa)
|
Tear-
strength (kN/m)
|
Viscosity
(After A/B mixed ,mPa.s)
|
Viscosity (After A/B mixed ,mPa.s)
|
Elongation(%) |
DC-15 |
white |
2 |
30-40 |
3-5 |
|
>3.5 |
>18 |
|
|
>500% |
Characteristics
*Good operability, easy to demold
*Moderate hardness
*High tensile and tear strength
*Cure at room temperature
*Good flexibility
*No oily
*High duplication times

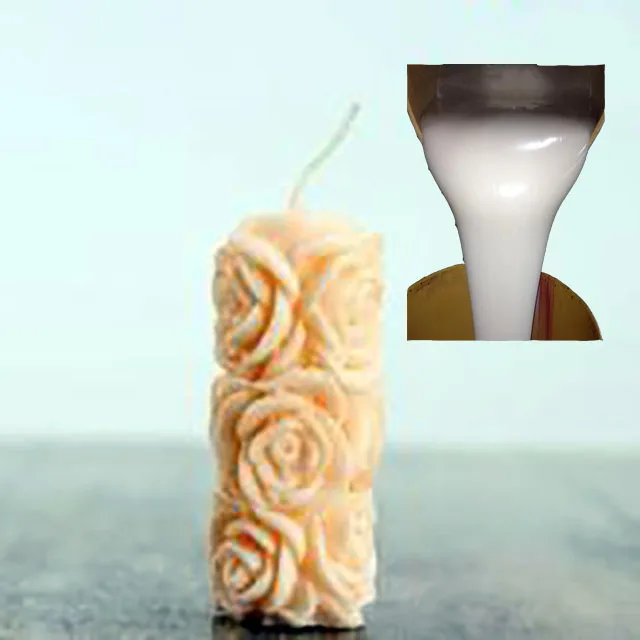
Operation Instructions
Operation instructions Step
Step 1: prepare the original molds Make your original molds perfect. fix it on a board. And fix the original mold on a board , then used four piece of board to enclose the original molds .
Step 2: Take 100 G parts A and add 2G parts B and mix them evenly.
*Notes: Mold making silicon rubber is a kind of flowing liquid ,it contains two parts. Part A is a kind of flowing white liquid and part B is the curing agent or catalyst .
Pls follow the step strictly:
1.Weigh the two part exactly by electronic weight. If not, for example add too much catalyst , the operation time will be too fast to operate ,which will cause inconvenience to operate .
2. Mix part A and part B evenly. Otherwise the silicon rubber will be partly solidified and this will give birth to difficulties in your final operation. What’s more, the finished molds will meet a short life. All of these will cause a waste of silicon rubber.
Step 3: Vacuum pumping Without exception, this step takes less than 10 minutes. Otherwise, it will cause cross linking reaction, and no more further steps will be available.
Step 4: Pouring casting or Brush operation
*Notes:1. For simple pattern products we suggest use pouring operation way, which will be very easy to operate and demould. Pourable silicone require low viscosity which will be easy to flow smoothly and easy to de-air .
2.For delicate pattern products we suggest use brushing operation way, which can copy the pattern exactly . Brushable silicone require high viscosity which won’t be easy to flow away and easy to brush .
3. We sugges to set the silicone mold for another 12 hours after demould before you put it into a large production .
Logistics Ways
According to different quantity of goods, logistic ways can be flexibly various from marine transportation, aerial transport and the express.
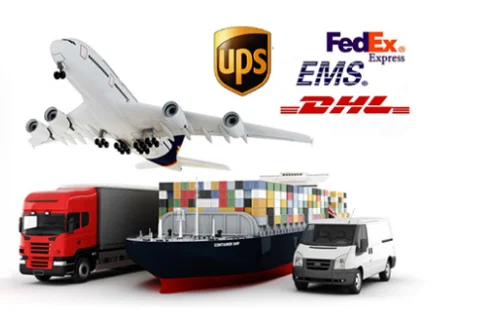
About Our Company
Shenzhen Zhihua Chemical Co.,Ltd.(DC SILICONE) was established in 2008,is a science and technology Company which is concentrating on production, R&D, and sales of Chemical products, especially silicone rubber.We are praised as the leading professional manufacturer of Mould Making Silicone Rubber, Addition Silicone Rubber ,Life Casting Silicone Rubber, Electronic Potting Compound, Pad Printing Silicone Rubber, and so on.There has two main Series of best selling silicone rubber in our company. The DC-A Series Addition cure silicone rubber and The DC- C Series Condensation cure silicone rubber.
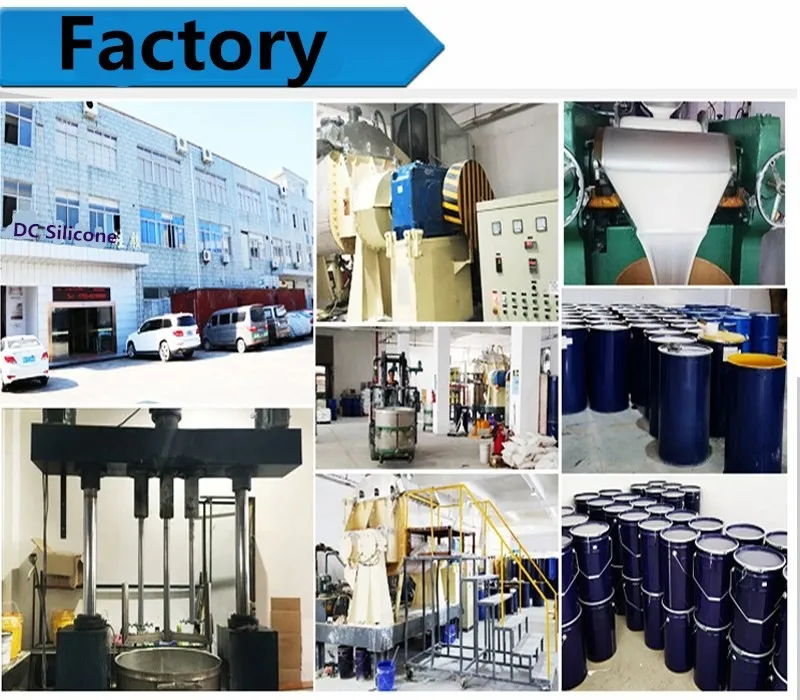
Package
25KG/drum vacuum packing for part A +1kg/ bottle catalyst for part B;9/18drums/pallet;
200KG/drum packing for part A +1kg/ bottle catalyst for part B; 1//2/4drums/pallet;
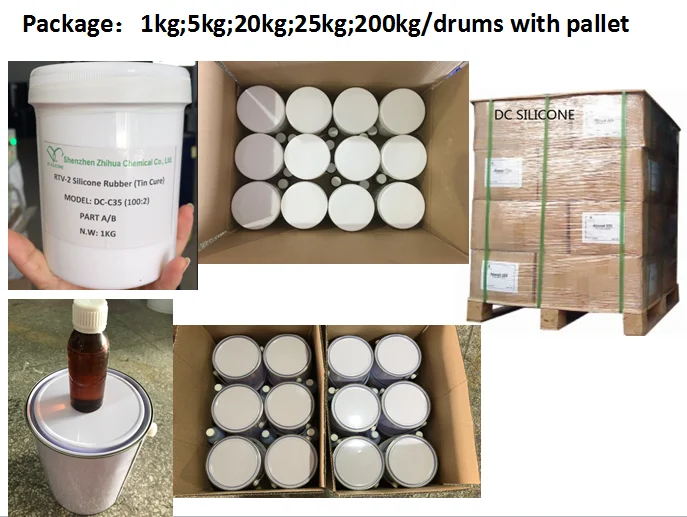
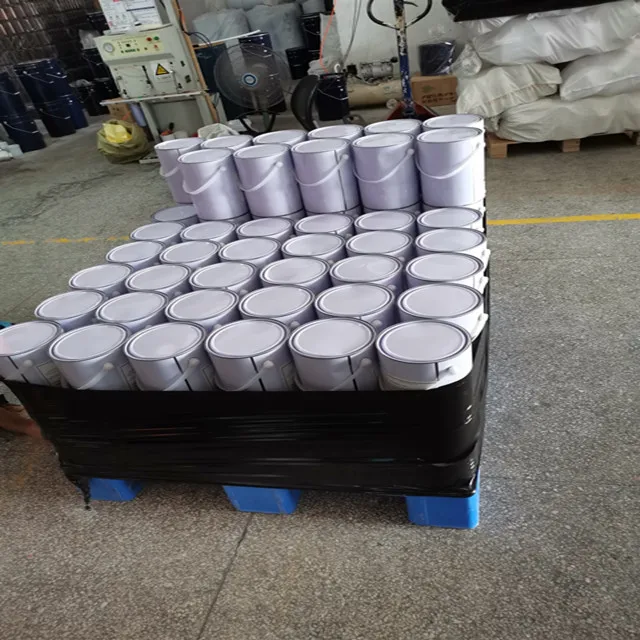
Shelf life
Twelve(12) months when stored under dry and cool place by original package under 25℃
Why choose us?
Attractive price to help you save cost
High quality with stable performance.
Free technical support and sample test to check the quality.
More than 10 years experience of silicone rubber producing.
Relate products purchasing assistance
New market developing
New products research and development Engineers Site Instruction Hardness can be customized according to your requirement
Color and package could be customized
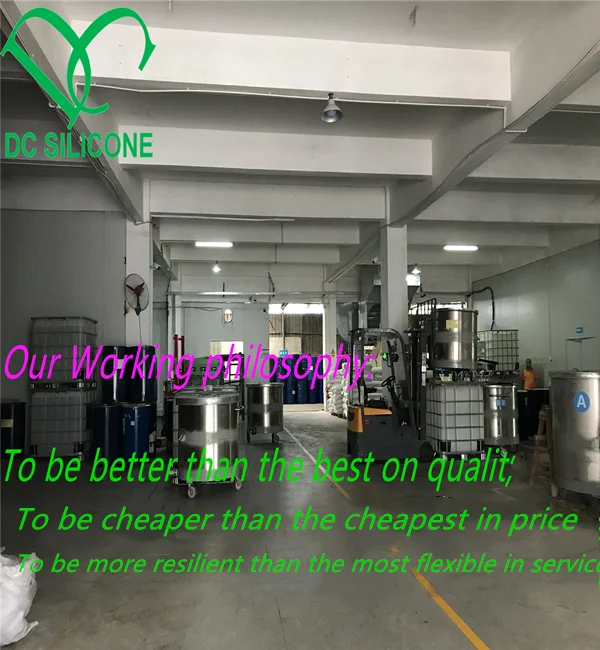
FAQs
Why could the silicone mold be reused only for a few times?
Maybe you will confuse about this question for years. Here we share you some following reasons:
- Addingtoo much silicone oil into silicone rubber. Silicone oil is an additive which will destroy the molecular weight of silicone rubber and reduce the tension and tear strength.
- Addingtoo much catalyst into the silicone rubber when you make the molds. For the condensation cure(tin catalyst) silicone rubber. we suggest you add no more than 2% of catalyst. If you 1add too much catalyst, the operation time will be too fast to operate ,which will also reduce the tension and tear strength.
- Using the silicon rubber with a high hardness to make molds for small sized products with delicate and intricate designs and the silicon rubber with a low hardness to makes molds for large sized products with simple designs.
Why does the silicone mold get burnt out?
The silicone mold get burnt out because you have left out the important notes when using unsaturated resin materials to produce your products. The unsaturated resin produces great heat when added the curing agent. So you must demould the product within 3 minutes to avoid this problem.
Our DC silicone rubber has add a special material which can resistant high temperature to make the resin molds. Help our customer avoid this problem.
Why does the silicone mould appear to be dry outside but wet inside?
Because molding silicone rubber is a kind of condensation silicone rubber, which get solidified after absorbing moisture from the air. In order to provide a significant shelf-life for the silicon rubber, we will dry out the water in the silicon rubber.
Solution: Add 0.05% water into the silicon rubber and Stir over a low speed briefly when you use it.
Why is the tear strength of the silicone mold weak?
There has three resons:
Firstly:In order to reduce the viscosity of silicone rubber and pursue a good quality, you may add a lot of silicone oil into the silicon rubber when making molds. In fact, it might have just the opposite effect. The tension and the tear strength will be reduced badly with the addition of silicon oil. And the silicon molds will be in a weak and flimsy manner.
Sencondly:you may add too much catalyst into the silicone rubber,we suggest customers add catalyst no more than 5%,2%will be perfect.
Thirdly:you may use the silicone mold too early after it finished.we suggest the customer begin using the molds after 24 hours. whatsmore,it will be better if you can make a outmold to protect the silicone mold.
Contact Us * Ms.Emily
Email: emily@dcsilicone.com
Mob & Whatsapp/Wechat: +86 13809730195